Thermal shock resistance is essential for facilities subjected to extreme and rapid temperature changes. Choosing the right flooring system ensures durability, cost-effectiveness, and safety in demanding environments.
Thermal Cycling and Thermal Shock Resistance
Thermal cycling refers to materials’ repetitive expansion and contraction caused by fluctuating temperatures. If the flooring is not designed to handle these stresses, it can lead to fatigue, cracking, and failure. On the other hand, thermal shock occurs when a material is exposed to sudden and extreme temperature changes, potentially causing immediate damage.
Facilities like food processing plants, commercial kitchens, and industrial freezers are particularly prone to these issues due to processes involving high-temperature steam cleaning or exposure to freezing conditions.
How Thermal Shock Resistance Applies to Resinous Flooring
Traditional epoxy systems often fail when exposed to thermal cycling or shock, leading to cracks, delamination, and costly repairs. Cementitious urethane systems like Sika PurCem, Ucrete, and Flowcrete Flowfresh are specifically engineered to withstand such stresses, offering superior performance in environments where thermal shock is a daily challenge.
These systems maintain their integrity even when subjected to rapid temperature changes. They can endure conditions where the floor experiences a temperature swing of up to 220°F or more within a short period, making them ideal for heavy-duty industrial environments.
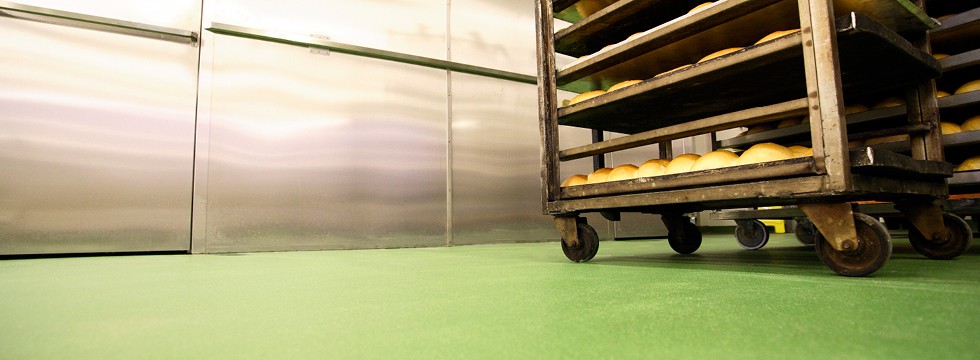
Why Some Materials Are Unsuitable for Thermal Shock Environments
Not all flooring materials are created equal. Choosing the wrong material for a thermal shock environment can lead to expensive and disruptive problems:
Epoxy Flooring Systems:
While durable under normal conditions, traditional epoxy is not flexible enough to withstand rapid temperature changes. Due to its rigid structure, epoxy tends to crack, delaminate, or fail when exposed to thermal shock.
Polyurethane Coatings:
Though flexible in some applications, basic polyurethane systems often lack the heat tolerance required for extreme environments and may discolor, degrade, or delaminate under high thermal stress.
Tile or Grouted Systems:
Due to differential expansion between the tile and grout during thermal cycling, tiles can crack or loosen, creating maintenance headaches and sanitation risks.
The Risks of Choosing Unsuitable Materials
- Costly Repairs: Frequent cracking and delamination increase repair expenses and facility downtime.
- Safety Hazards: Damaged flooring can become slippery, uneven, or unsanitary, posing risks to workers and compliance violations.
- Shortened Lifespan: Materials not designed for thermal shock will fail prematurely, requiring frequent replacements and inflating lifecycle costs.
The Bottom Line: Cutting corners on materials that aren’t built for thermal shock environments can result in significantly higher costs over time, disruptions to operations, and safety risks.
Which Cementitious Urethane Should You Choose?
Temperature resistance can vary based on factors like application thickness and specific operational conditions. A simple guide to selecting the right flooring system based on temperature and application requirements will help you make an informed choice:
PurCem:
Sika’s PurCem® flooring systems are engineered to withstand a broad range of temperatures, making them suitable for various industrial applications. PurCem 19NA, 20NA, or PurCem 22: Handles heavy-duty applications with thermal cycling up to 248°F. These products are designed to maintain their physical properties across a wide temperature range, from -40 °C (-40 °F) up to 120 °C (248 °F), making them ideal for environments subject to thermal shock and thermal cycling.
Ucrete:
Ucrete MF: Ideal for moderate temperature swings, up to 250°F. Ucrete HF60RT: Perfect for heavy-duty industrial floors, tolerating up to 392°F. For environments with higher thermal demands, consider systems like Ucrete® UD200, which can withstand continuous exposure up to 130°C (266°F) and occasional spills up to 150°C (302°F).
Flowfresh:
Flowfresh SL: Seamless, chemical-resistant system designed for thermal cycling up to 212°F. Flowfresh HF: Heavy-duty screed capable of withstanding high temperatures up to 284°F.
Should You Consider Thermal Shock-Resistant Flooring?
Therm shock-resistant flooring is a must if your facility involves processes that subject floors to rapid or extreme temperature changes—such as steam cleaning, boiling liquids, or icy conditions.
- Prevents Damage: Protects against cracks and delamination caused by temperature fluctuations.
- Reduces Costs: Minimizes repair and maintenance expenses over the long term.
- Enhances Safety: Provides a seamless, slip-resistant surface that meets strict safety and hygiene regulations.
Conclusion
Installing a thermal shock-resistant flooring system like Sika PurCem, Ucrete, or Flowfresh ensures your floors can handle the toughest conditions without compromising performance or aesthetics. Whether you’re managing a food plant, brewery, or pharmaceutical facility, the right flooring solution will solve problems and add long-term value to your operations.